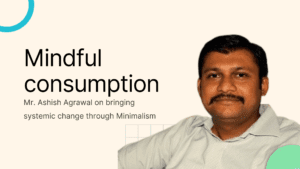
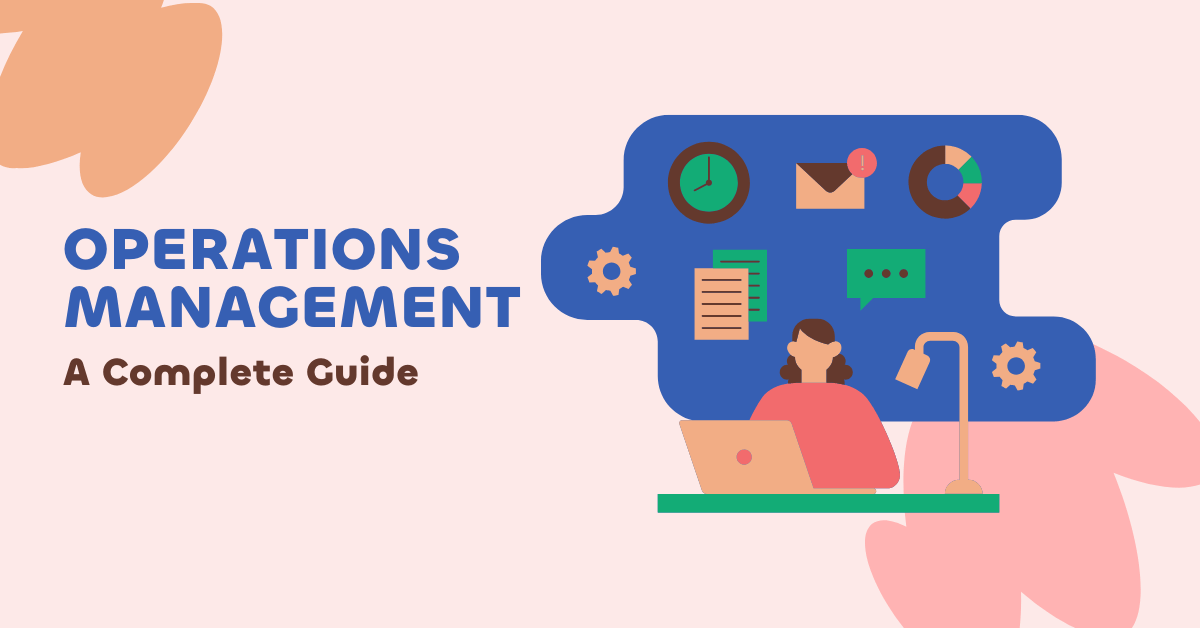
Contents
Operations management is the backbone of any successful business, focusing on efficiently transforming resources into products or services that meet organizational goals. From planning and organizing to executing and improving processes, it ensures that every aspect of production or service delivery runs smoothly. This discipline plays a critical role in reducing costs, optimizing resource use, and maintaining high standards of quality. Whether it’s in manufacturing, healthcare, retail, or technology, operations management is essential for driving efficiency and sustaining business growth.
Well, this blog talks about what operations management entails and how it impacts businesses across various industries.
What is Operations Management?
Operations management is the discipline of designing, overseeing, and optimizing the processes involved in producing goods or delivering services. It ensures that all resources—including labor, materials, technology, and time—are used efficiently and effectively to meet organizational goals.
Think of operations management as the behind-the-scenes engine that keeps a business running smoothly. It focuses on transforming inputs (like raw materials, human effort, and capital) into outputs (finished products or services) while maintaining quality and minimizing costs.
Key elements of operations management include:
- Planning: Setting goals, forecasting demand, and preparing resources to meet objectives.
- Organizing: Arranging tasks, assigning responsibilities, and coordinating efforts across teams.
- Executing: Implementing plans, monitoring progress, and ensuring workflows are uninterrupted.
- Improving: Continuously analyzing and enhancing processes to boost efficiency and adapt to market changes.
Operations management is vital for any industry, whether it’s manufacturing, healthcare, retail, or technology. For example:
- In manufacturing, it involves streamlining assembly lines and managing supply chains.
- In healthcare, it ensures that hospitals are adequately staffed and that patients receive timely care.
- In retail, it focuses on inventory control, store layouts, and customer service.
Ultimately, operations management bridges the gap between strategy and execution, ensuring that organizations can deliver on their promises while staying competitive in their markets.
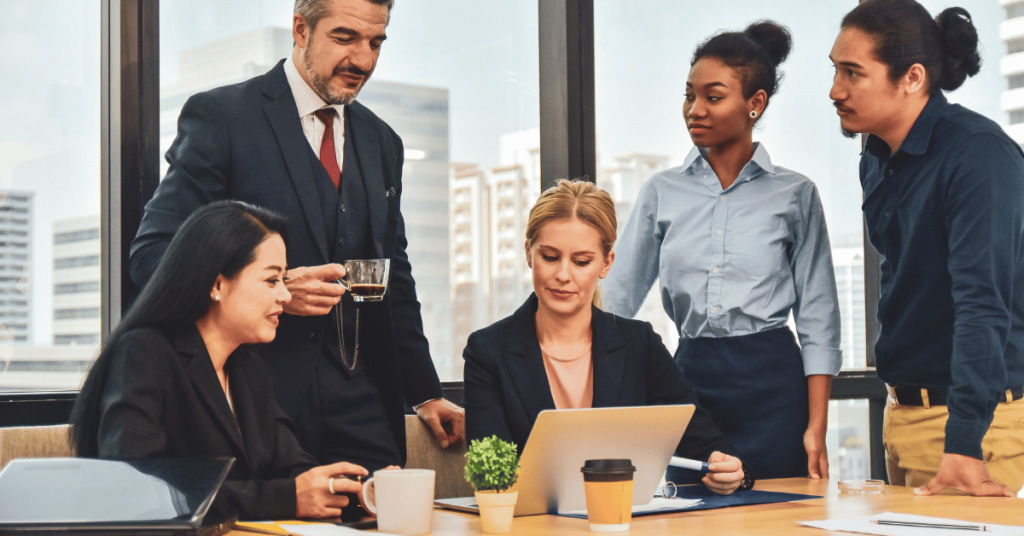
Operations Management Examples
Operations management plays a pivotal role across various industries, ensuring that processes run smoothly, resources are optimized, and quality standards are met. Here are some real-life operations management examples of how it is applied in different sectors:
- Manufacturing: At a car factory, operations management ensures the right parts are delivered just in time, assembly lines work efficiently, and every car meets high-quality standards.
- Healthcare: In hospitals, operations management oversees staff schedules, ensures equipment is functional, and makes sure patients receive timely care.
- Retail: Supermarkets use operations management to keep shelves stocked, reduce checkout lines, and optimize store layouts for better customer flow.
- Technology: In software companies, operations management coordinates teams to meet project deadlines and ensures all tools are functioning properly.
- Logistics: For delivery companies, it’s about planning routes to save fuel and time while ensuring packages reach their destinations on schedule.
Role of Operations Management in an Organization
Operations management plays a pivotal role in ensuring the smooth functioning of an organization. By streamlining processes and managing resources effectively, it helps achieve strategic objectives and deliver value to customers. Here’s a breakdown of its key roles:
1. Enhancing Efficiency
Operations management identifies and eliminates bottlenecks in workflows, ensuring optimal use of resources like time, labor, and materials. This reduces waste and increases productivity across the organization.
2. Ensuring Quality
Maintaining high-quality standards is crucial for customer satisfaction and business success. Operations management implements quality control measures and continuously monitors production or service delivery to meet or exceed expectations.
3. Cost Control
Effective operations management helps organizations identify cost-saving opportunities without compromising quality. It ensures that resources are utilized judiciously, reducing expenses and increasing profitability.
4. Driving Innovation
By analyzing processes and adopting the latest technologies, operations management fosters innovation. This helps organizations stay competitive and adapt to market trends.
5. Aligning with Organizational Goals
Operations management ensures that all departments and processes are aligned with the company’s strategic objectives. It bridges the gap between planning and execution, enabling the organization to achieve its mission and vision.
6. Improving Customer Satisfaction
Smooth operations lead to timely delivery of products and services, meeting customer expectations. Operations management focuses on creating a seamless experience, which helps build loyalty and trust.
7. Compliance and Risk Management
Operations management ensures adherence to legal, environmental, and safety standards. It also identifies potential risks in processes and implements measures to mitigate them.
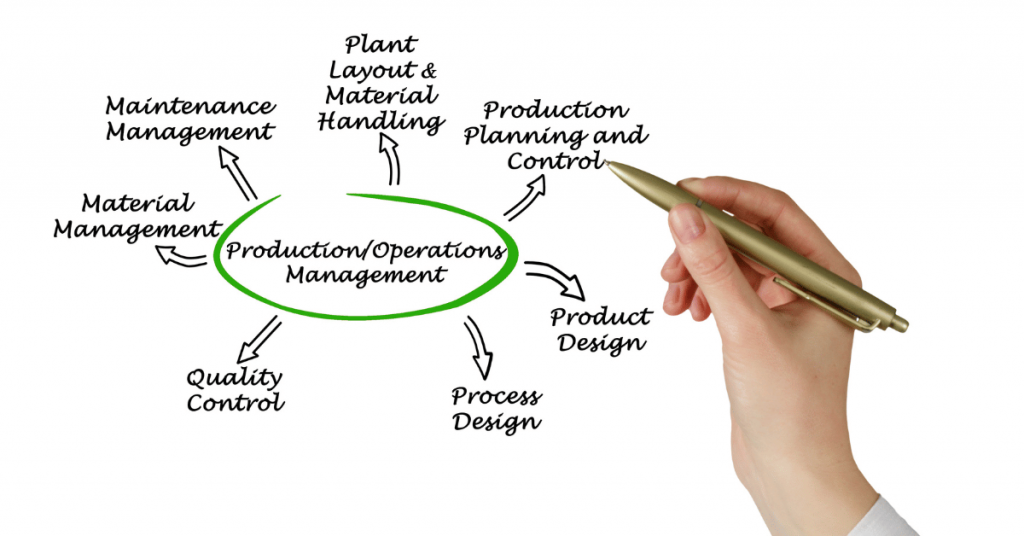
The Operations Management Process
The operations management process is a systematic approach to managing resources, workflows, and activities to produce goods or deliver services efficiently. This process ensures that an organization’s operations align with its strategic goals while maintaining quality and optimizing costs. Below is a breakdown of the key stages in the operations management process:
1. Planning
This is the foundation of operations management. It involves:
- Setting clear objectives and determining the resources needed.
- Forecasting demand for products or services.
- Developing strategies to meet customer expectations within budget and time constraints.
2. Organizing
Once plans are in place, the next step is organizing:
- Assigning tasks and responsibilities to teams or individuals.
- Allocating resources like equipment, materials, and budgets.
- Designing workflows to ensure smooth operations.
3. Staffing
People are a critical component of any operation. Staffing includes:
- Recruiting and hiring skilled employees.
- Providing training to enhance their capabilities.
- Ensuring workforce availability to meet operational demands.
4. Leading
Leadership ensures that operations are carried out as planned. This involves:
- Motivating employees to perform at their best.
- Resolving conflicts and addressing challenges.
- Communicating goals and expectations clearly.
5. Controlling
Controlling ensures that operations stay on track. It includes:
- Monitoring performance through key metrics and benchmarks.
- Identifying deviations from the plan and implementing corrective actions.
- Evaluating outcomes to improve future processes.
What Does an Operations Manager Do?
An Operations Manager is responsible for overseeing the day-to-day activities of a business or organization to ensure smooth and efficient operations. Their primary role is to manage resources, processes, and teams to optimize productivity, meet business goals, and improve performance. Here are the main duties of an Operations Manager:
- Process Management: Streamlining operational processes to ensure efficiency and effectiveness.
- Resource Allocation: Ensuring the proper allocation of resources, including personnel, equipment, and materials.
- Team Management: Supervising and leading teams, ensuring they meet performance standards and achieve company goals.
- Budgeting and Cost Control: Managing budgets and controlling operational costs to maintain profitability.
- Quality Assurance: Ensuring the quality of products or services meets company standards and customer expectations.
- Supply Chain Management: Overseeing inventory, procurement, and distribution processes.
- Problem Solving: Identifying and addressing operational challenges or bottlenecks.
- Reporting and Analysis: Monitoring performance metrics and generating reports to inform decision-making and drive improvements.
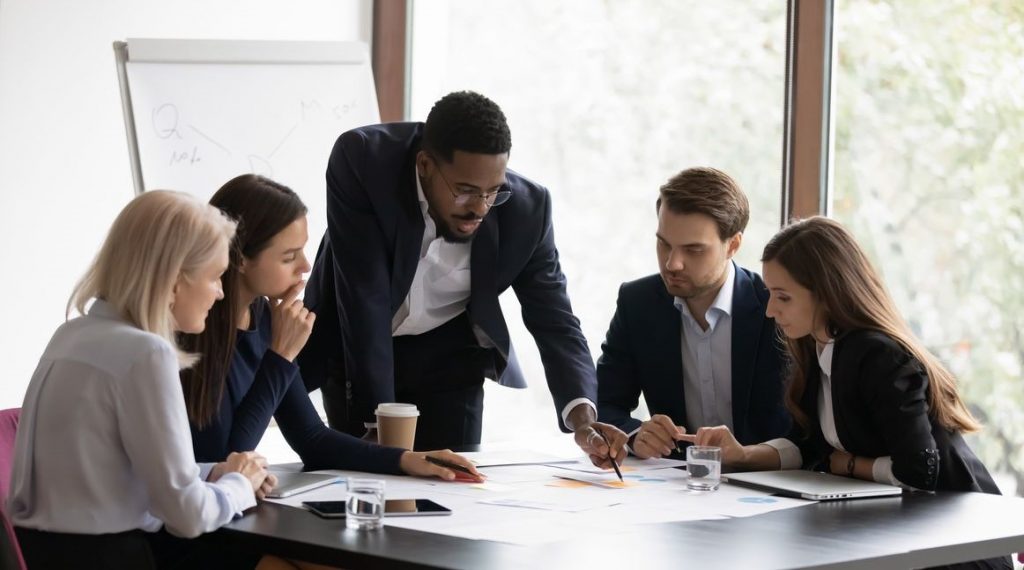
Operations Management Examples: The Process
Operations management involves a variety of processes that ensure the efficient functioning of an organization. Here are some common processes with operations management examples:
- Supply Chain Management: This process involves managing the flow of goods and services from suppliers to customers. It includes procurement, logistics, inventory management, and distribution.
- Production Planning: This process focuses on scheduling production to meet demand efficiently while optimizing resources, such as labor, equipment, and raw materials.
- Quality Control: Ensuring products or services meet predefined quality standards through regular inspections, testing, and corrective actions. This process helps maintain customer satisfaction and compliance with regulations.
- Inventory Management: Involves monitoring and controlling the inventory levels of raw materials, work-in-progress, and finished goods to avoid stockouts or overstocking while minimizing costs.
- Process Improvement (Continuous Improvement): Operations managers regularly review and improve operational processes to increase efficiency, reduce waste, and enhance product quality, often using methodologies like Lean or Six Sigma.
- Capacity Planning: This process involves determining the production capacity needed to meet demand. It ensures that there are enough resources, facilities, and equipment to produce goods or services on time.
- Resource Allocation: Allocating human, financial, and physical resources in a way that maximizes efficiency and aligns with organizational goals. It includes staffing, budgeting, and equipment management.
- Demand Forecasting: Predicting future customer demand to ensure the organization can meet it without overproducing or underproducing, helping manage inventory levels and production schedules.
- Maintenance Management: Ensuring that machinery and equipment are maintained and repaired regularly to minimize downtime and avoid disruptions to production.
- Risk Management: Identifying and managing potential risks to operations, such as supply chain disruptions, equipment failures, or regulatory changes, and developing contingency plans.
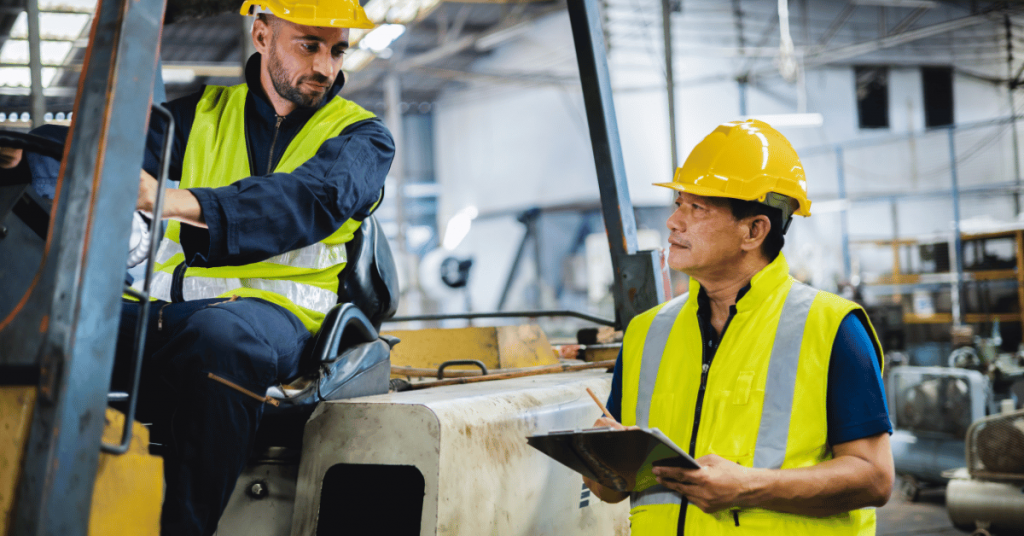
Real-Life Examples
Here are some real-life examples of operations management processes in action across various industries:
1. Supply Chain Management - Apple
Apple is known for its efficient supply chain management. They maintain close relationships with suppliers worldwide, ensuring they have the raw materials needed for production. Apple uses a just-in-time (JIT) inventory system, ensuring that products are manufactured based on demand forecasts, minimizing excess inventory and reducing costs.
2. Production Planning - Toyota
Toyota uses the Toyota Production System (TPS), which focuses on lean manufacturing and waste reduction. A key aspect is Jidoka (automation with a human touch), which allows workers to stop the production line if there’s an issue, ensuring quality control. Production is planned based on customer demand, and flexible manufacturing systems allow Toyota to produce different models in a streamlined process.
3. Quality Control - McDonald's
McDonald’s has a well-established quality control process across its global network. Each restaurant must adhere to strict quality standards for food preparation and service. For instance, McDonald’s uses detailed checklists for food safety, ensuring that cooking temperatures and food handling procedures meet health regulations and customer expectations consistently.
4. Inventory Management - Amazon
Amazon employs advanced inventory management systems and robotics in its warehouses to ensure efficient stock control. With millions of items in inventory, Amazon uses algorithms to predict demand and optimize stock levels, reducing the chances of stockouts or overstocking, and speeding up order fulfillment.
5. Process Improvement (Continuous Improvement) - GE (General Electric)
GE is known for its commitment to continuous improvement through its Six Sigma program. In the 1990s, GE’s CEO Jack Welch made Six Sigma a central part of the company’s strategy to eliminate defects and improve operational efficiency. Engineers at GE would work to improve processes by analyzing data, finding areas of waste, and proposing solutions that could save the company millions of dollars.
Mission Sustainability: Operational Efficiency Services
Mission Sustainability focuses on optimizing business operations to achieve both environmental and operational goals. These services help organizations improve resource utilization, reduce waste, and integrate sustainable practices across their operations. From energy management and waste reduction to supply chain sustainability and eco-friendly technology integration, our approach ensures that businesses not only enhance efficiency but also contribute to a greener, more sustainable future. Their services include:
- Process Optimization: Pinpointing inefficiencies and fixing them to save time and resources.
- Resource Management: Advising on smarter ways to use materials, energy, and manpower.
- Sustainability Practices: Introducing eco-friendly methods to improve operational efficiency without harming the planet.
These services not only help businesses grow but also ensure they contribute positively to society. To learn more, visit Mission Sustainability.
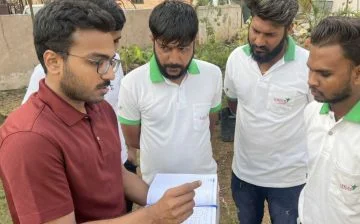
Why is Operations Management Important: The Benefits
The benefits of operations management are crucial for several reasons, as it directly impacts a company’s efficiency, profitability, and competitiveness. By optimizing processes and resources, operations management ensures that businesses can meet their goals while minimizing waste and reducing costs. Here are the key reasons why operations management is important:
1. Optimizes Efficiency
Operations management ensures that resources—such as labor, materials, and machinery—are used effectively, reducing waste and maximizing productivity. This leads to smoother workflows and cost-effective processes.
2. Enhances Product Quality
Through quality control and continuous improvement processes, operations management helps maintain high standards, ensuring products meet customer expectations and regulatory requirements.
3. Cost Control
By managing processes, optimizing resource allocation, and reducing inefficiencies, operations management helps keep costs under control, improving a company’s bottom line.
4. Customer Satisfaction
Effective operations management ensures timely production and delivery of goods and services. Meeting customer demands quickly and reliably fosters loyalty and boosts customer satisfaction.
5. Competitive Advantage
Companies that excel in operations management can deliver products faster, at lower costs, and with better quality, which helps them gain an edge in the market.
6. Supports Growth
Well-managed operations create the foundation for scalability, allowing businesses to expand smoothly without sacrificing quality or efficiency.
7. Risk Management
Operations management involves identifying potential risks in the supply chain, production processes, or workforce management, helping businesses prepare and mitigate those risks.
8. Innovation
It encourages the adoption of new technologies, processes, and methodologies (like automation, AI, and Lean practices), which drive continuous improvement and innovation in products and services.
Final Thoughts
Operations management is a vital aspect of any organization’s success. By focusing on enhancing efficiency, ensuring quality, and minimizing costs, it helps businesses meet their objectives and stay competitive in the market. From small businesses to large corporations, effective operations management ensures that processes run smoothly, customer satisfaction is prioritized, and long-term growth is achievable. For businesses striving to succeed, mastering operations management is the key to sustaining operational excellence.
FAQs
1. What is meant by operations management?
Operations management involves planning, organizing, and overseeing the production of goods and services to optimize efficiency, reduce costs, and meet business objectives.
2. What are the 4 types of operations management?
The four main types of operations management are:
- Manufacturing: Producing goods efficiently.
- Service: Delivering intangible services.
- Logistics: Managing movement and storage of goods.
- Project: Managing specific projects from planning to completion.
3. What are the 7 main functions of operations management?
The seven key functions of operations management are:
- Product Design
- Quality Management
- Process Management
- Supply Chain Management
- Inventory Management
- Scheduling
- Maintenance Management
Related articles
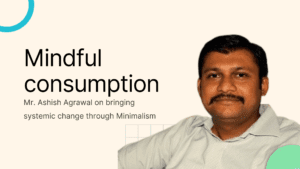

Transforming Lives and Waste Management in Bengaluru – Hasiru Dala Innovations’ Journey
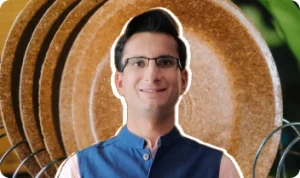